Reduce wear on hydraulic seals and gaskets
- Rexroth Distributors
- Sep 15, 2022
- 4 min read
Replacing seals and gaskets is an unavoidable part of ensuring optimal function of hydraulic systems. Proper sealing goes a long way in reducing contamination in the Rexroth hydraulic pump.
However, there are steps you can take to reduce wear between replacements and extend the life of these integrated components.
When planning preventative measures of any kind, it helps to identify and understand the external factors that influence wear on your system. A good understanding of why Rexroth pump fail helps you plan ways to avoid failure and extend replacement cycles.
In this article, we will start by looking at environmental, environmental, and compatibility factors that affect seal wear. Next, we will comment on the indications for the correct installation and maintenance of the seal and gasket.
The repayment period can be prolonged by first minimizing the effects of each of the following factors and proceeding with expert care.
Environmental factors
Select seals and gaskets that meet the needs of external forces. For example, your choices should consider these factors:
Friction
Download and compress
Pressure
Knowing these sealing and fitting dynamics will help make the right decisions and reduce wear in the future. We cover each of them in more detail below.
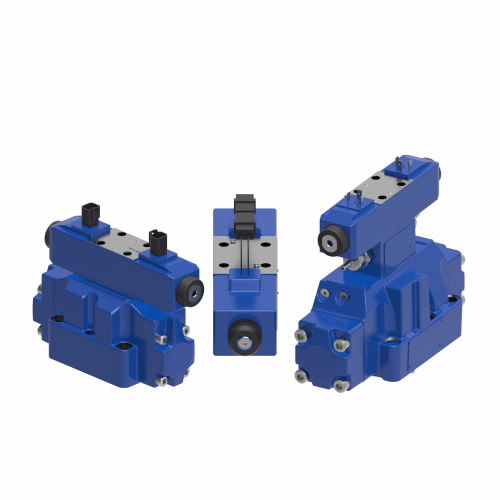
Environmental Factor #1: Friction
Let's look at two types of friction: excessive friction and excessive friction during running.
Excessive friction can cause high hydraulic pressure and excessive friction during operation can cause heat and swelling. The important facts to know are that penetrating friction decreases as sealant, gasket, or O-ring stiffness decreases, and friction during operation decreases as sealant, gasket, or gasket stiffness increases. Tori
Environmental Factor #2: Pregnancy and Stress
The next consideration is the load and pressure, and the springbuck required to return the tampons to their original shape. Load tolerances must be considered for all parts in contact with sealing applications to create a solid seal.
Also, springbuck must be observed once the compressive force is removed to prevent compression set (which is the failure of the seal to return to its original shape).
Environmental Factor #3: Stress
Higher pressures, especially those above 5,000 psi, require special seals with a higher modulus of elasticity and stiffer materials. If the part material cannot withstand the increased high pressure, it can quickly cause wear that can lead to premature failure, leaks, and system contamination.
Other options for O-ring selection may be considered, such as using replacement O-rings or reducing diagonal clearance. Learn more about this here.
Surrounding factors
Environmental conditions that should be examined as part of creating your Eaton hydraulic valve Rexroth a4vg corrosion prevention plan include the following three items:
Temperature
Radioactive contamination
Exposure to ultraviolet rays
Considering these factors when choosing materials and designs will help you choose components that better resist wear and tear and increase the time between replacements.
Here's why it's important to consider these factors and their negative effects when choosing seals and gaskets:
Temperature – Excessive heat will cause the material to swell and harden, while cold temperatures can cause shrinkage and leakage.
Contamination: Contamination from hydraulic fluids, such as metal chips, can damage seals and gaskets.
UV Exposure – Rubber materials can crack, lose elasticity, fade, and disintegrate with continued exposure to UV rays (from the sun, lamps, or even lasers)
Compatibility factors
Regardless of knowledge of external and local factors, if seals and gaskets are chemically incompatible, early wear is evident.
Make sure the product is compatible with the sealing and gasket materials to avoid this, and always choose the materials that offer the best chemical resistance.
You'll want to know what specific chemicals are in your hydraulic system, and be sure to choose a design that protects against harsh chemicals (such as strong acids or alkalis). A good material compatibility guide will help with this decision.
Installation and maintenance
Proper installation and maintenance of Rexroth valve and seals is vital to their longevity. After selecting the appropriate gasket or seal that meets the environmental, environmental, and machine compatible needs, installation and maintenance procedures must be determined.
Seals
The installation procedure may vary depending on the nature of the seal application. However, it is universally known that some initial tips increase the life of a part after correct installation.
Before installing:
Have the proper tools on hand to avoid dents or damage.
Be sure to clean the stamps with a lint-free cloth.
Protect seals from sharp corners and burrs
Lubricate the seal and its sealing path
Heating seals to lubricate and improve flexibility
Regular lubrication checks are recommended to ensure that the material can withstand environmental and environmental factors.
Boards
Procedures for installing gaskets correctly include:
Align flange faces and screw holes and check for irregularities
Carefully insert the gasket between the dry lips
Make sure that the gasket is placed in the middle between the flanges
Assemble the flanges together, making sure the gasket is not compressed or damaged.
Keep the gaskets handy and clean them with a soft towel or sponge in warm, soapy water every week. Do not use bleach, degreasers, disinfectants, or commercial washers.
Finally
These maintenance and installation tips, along with the proactive and well-planned selection of materials that meet the needs for friction, load, pressure, temperature, contamination, and UV exposure, will dramatically reduce damage and increase Rexroth hydraulic valve efficiency and overall performance.
By taking the time to consider these factors, as well as seal and gasket material compatibility, and maintaining parts function, wear between replacements can be reduced. This will increase cycles between component replacement and reduce the chance of hydraulic system failure.
Comments